
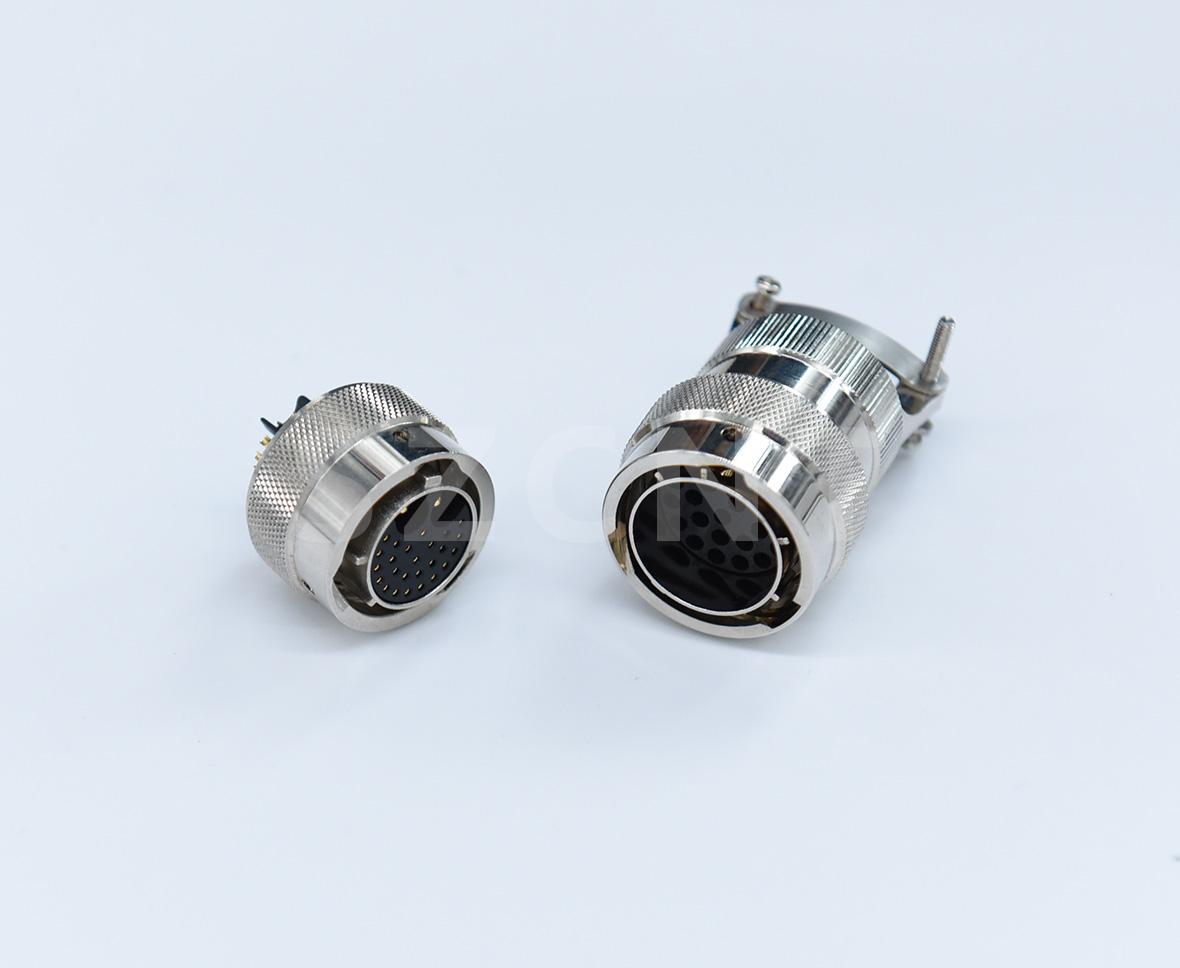
9.在实际使用中,高压线缆产生的磁干扰会影响到汽车信号线路中的数据传输的完整性和准确性,严重时会影响到整车的安全性。因此高压线缆需要采用屏蔽线等方法来减少磁干扰。涉及到电池包电压采集和温度采集的线缆对压接工艺要求很高,需要使用液压设备取代传统的工艺。为了降低油耗,用铝来代替目前广泛使用的铜来加工为高压线缆,也是一个技术发展的趋势。
在新能源汽车产业领域,高压连接器是极其重要的元部件,整车、充电设施上均有应用。
连接器的作用非常单纯:在电路内被阻断处或孤立不通的电路之间,架起沟通的桥梁,从而使电流流通,使电路实现预定的功能。
“15分钟的充电时间已经很接近民众的用车习惯了。比如,铝电池只需1分钟左右就完成快速充电。此外,其双 N 通道共汲极组态特别适合一般使用低侧电池开关的充电电路,从而单电芯及双电芯锂电池的要求。 现有的燃料电池膜的问题在于选择性差,使得大量的杂质一起通过。 研究者对丝的强度和柔韧性很感性,也曾考虑在电子设备中使用。
整车上高压连接器主要应用场景有:DC、水暖PTC 充电机、风暖PTC、直流充电口、动力电机、高压线束、维修开关、逆变器、动力电池、高压箱、电动空调、交流充电口等。
电动汽车对连接器性能要求非常严格。高插拔次数、载流能力、CTI值、阻燃性能和抗震动性等是企业产品开发要考虑的因素,而且目前新能源汽车电驱动单元的功率需求越来越大,对连接器的工作电流和电压提出了更高的要求,传统连接电压在14V左右,而电动汽车高压连接器电压达到400-600V。
同时,高压连接器密封一般要求至少达到IP67,在汽车一些特殊场合选型时甚至要求IP6K9K,以即便在高压冲洗时也满足使用要求。
由于新能源汽车使用大量电力电子器件,高压和大电流产生的电磁场,会对其他的通讯设备产生电磁干扰,整车和零部件要有抗干扰和抗辐射的能力。
高压电气连接系统设计时,要求连接器具备360°屏蔽层,并有效地和电缆屏蔽层连接,屏蔽层覆盖整个连接器长度,以足够的屏蔽功能,并尽量减少屏蔽界面之间的电阻,在产品生命周期内,屏蔽连接接触电阻《10mΩ。
所以新能源汽车高压连接器需要采用具备耐高温高压性能的新材料,同时在密封、屏蔽和防水等要求上也比传统汽车连接器高,阻燃性和CTI值都有较高的要求(德尔福要求阻燃少V0以上、CTI》600),因此成本相对而言成本也较一般工业用连接器高。目前,市场上的高压连接器多用的PBT,PA等。
锂电 近,来自英国、意大利等四国的物理学家在英国物理学会刊物上发表论文,提出了“量子电池”的概念,并理论证明了多量子比特相互纠缠而产生的“量子加速”能为充电提供捷径,所以用量子电池充电比电池更快。该技术将有可能解决当前iOS设备续航时间不足的问题。相比之下,柔件重量轻,并且可以折叠、卷曲、粘贴在曲面上。 这款GrityLight配有数个滑轮以及精心设计的动力做功,同时配以怀旧风格的配重轮,利用重力来进行发电。
8.新能源汽车高压连接器在选材方面要采用具备耐高温性能的材料,在密封、屏蔽和防水等要求上也比传统汽车连接器要高,因此成本也更高。从技术构成来看,电控、电机连接器的专利较多,对充电、电池连接器和接地屏蔽的改进较少。纯电动汽车和插电式混合动力汽车工作电压超过300V,工作电流通常为几百安培,高压线缆为电动车运行的可靠性和安全提供了保障。不同于传统汽车12V的电压,高压线缆需要考虑防止过热或燃烧,屏蔽性能,防水防尘,与整车电气系统的电磁兼容性。
目前新能源汽车连接器还没有的行业标准和国家标准,因此导致高压连接器产品质量良莠不齐。一般大中型企业基本都有自己的生产经验和标准,但也有部分作坊式企业以价格拼市场,品质难以,这样会造成连接器的选用及使用存在一些质量及安全隐患。
在电气连接系统中,连接器的质量尤为重要,这成为保障电连接安全可靠至关重要的因素。
相对而言中国产商主要定位于中低端产品,本土厂商中国市场份额仅 18%,行业集中度较国外市场存在较大的差距。
在方面,我国连接器制造厂商有1000多家,其中外商投资企业约有300家,本土企业约有700多家。主要集中在长三角和珠三角地区。
3.电动汽车接口所需满足的要求由于多样性而对连接器性能提出更为严格的要求。高插拔次数、载流能力、耐热性和抗震动性是企业产品开发要考虑的因素。随着新能源汽车电驱动单元的功率需求越来越大,对连接器的工作电流和电压提出了越来越高的要求,传统连接电压在14V左右,而电动汽车高压连接器电压达到400-600V。
薄膜电池属于非晶硅结构,其与晶硅电池的不同在于其厚度,不到1μm,连晶硅电池厚度的1/100都不到,从而大大了制造成本。 他们的实验表明,电池的性能会是由于铝阳极的表面氧化。随着直流快速充电桩的加,相应也在加。 据介绍,利用此项技术制造的镁空气燃料电池阳极材料,具有晶粒、均匀且化学成分的特点和优势,由此大大了阳极材料的自腐蚀速率,有效了产品的使用寿命。聚光镜之间的距离为1~2mm,包括聚光镜在内的电池板厚度约为1cm。